Blog
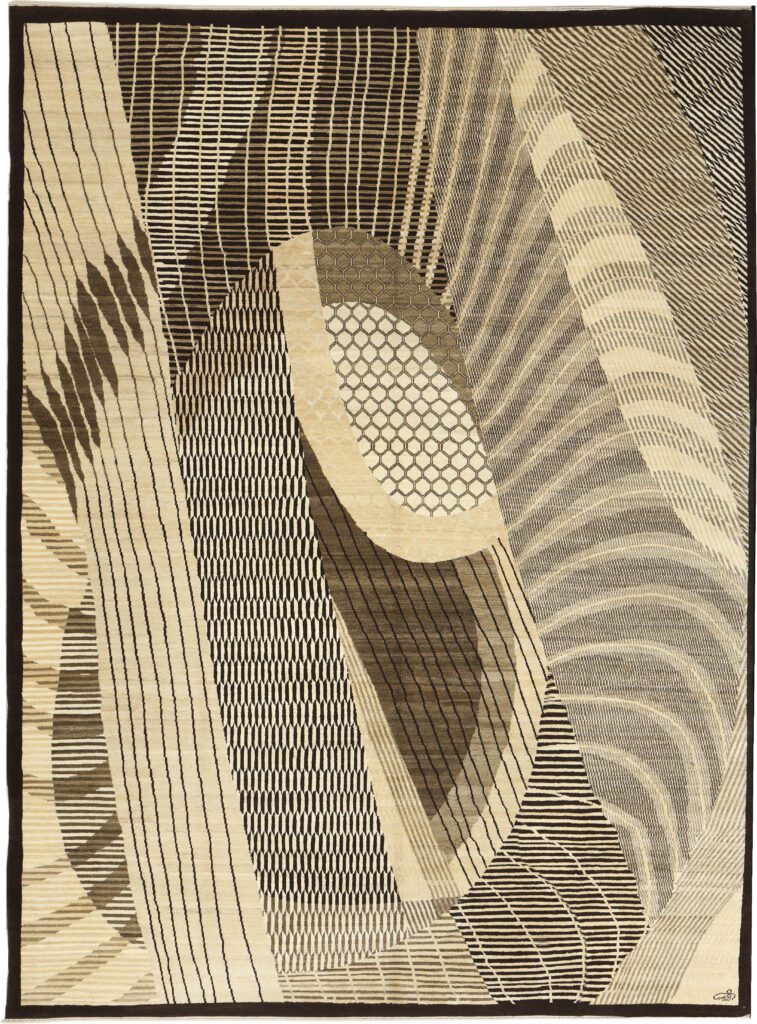
Staff Pick: Harmony – A Visual Symphony in Wool
Reviving an old regular blog post, this week's Staff Pick focuses on the stunningly composed "Harmony" from the Orley Shabahang Music Series Some rugs make you pause. Harmony does more—it...
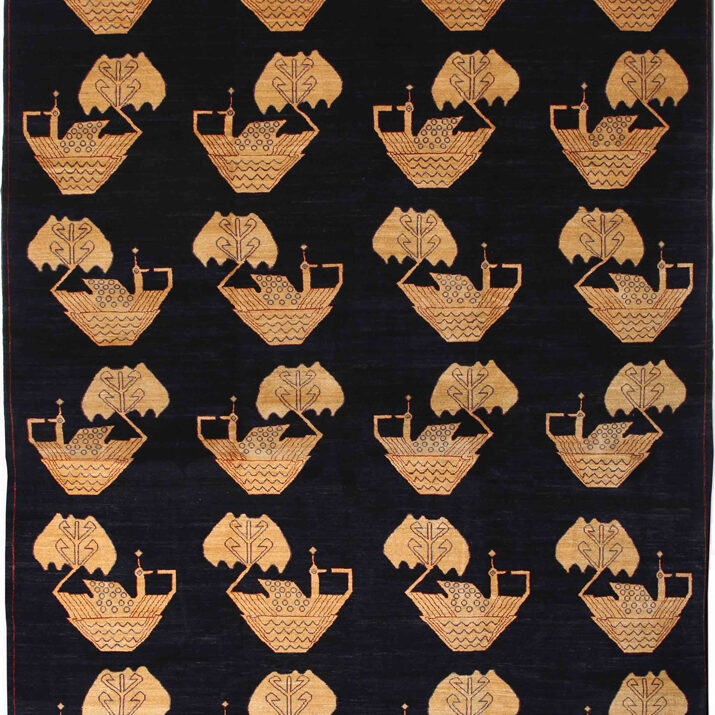
Animal Collection Rugs: Reviving Tradition Through Modern Design
Classic Persian peacock motifs fill the space in a contemporary colorway and pattern, a striking example of our Animal Collection's inspiration From the heart of ancient Persia to modern interiors,...
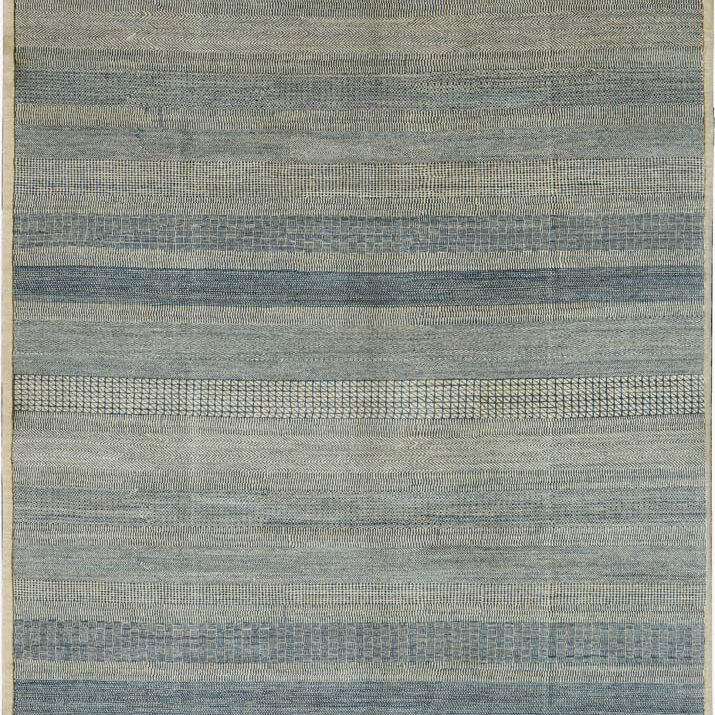
Rain Collection: The Art of Rain in Motion
In blue on cream, Rain showcases its stunning minimalist contemporary design Rain falls, gathers, flows, and disappears—only to return again. It streaks through the sky, ripples in puddles, and carves...
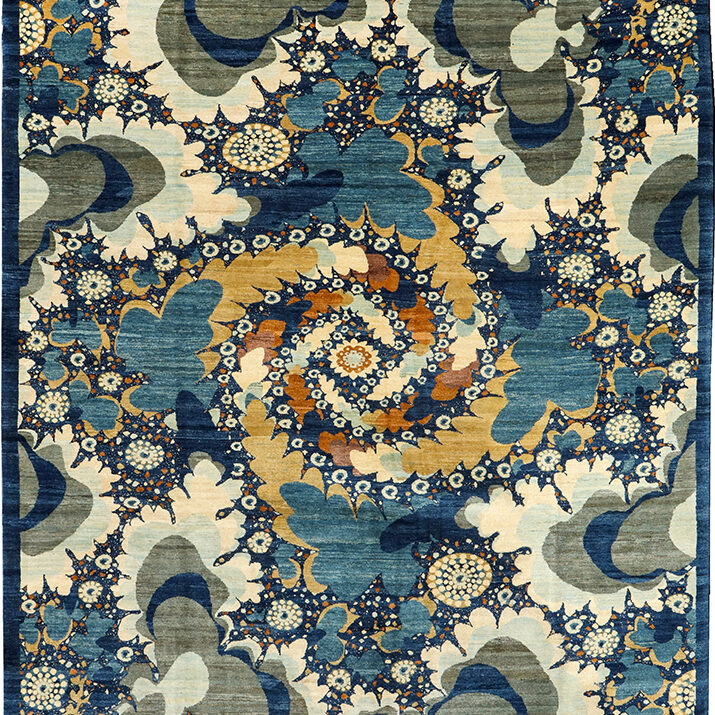
Galaxy Series Rugs: The Beauty of Fractals in Motion
Featuring the spiral motifs central to our Galaxy Collection, Nocturne stuns and soothes at the same time in calming blue hues. From the vast reaches of space to the smallest...
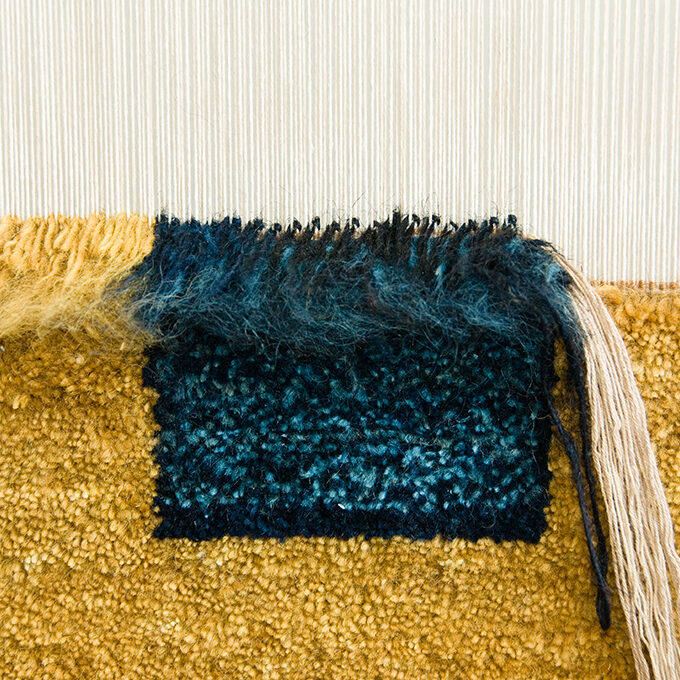
Bespoke Rugs and Their Unique Beauty
Handknotted carpet on the loom mid weaving When you imagine the perfect bespoke rugs, what do you see? Perhaps it’s vibrant centerpieces that reflect your bold style, or subdued and...
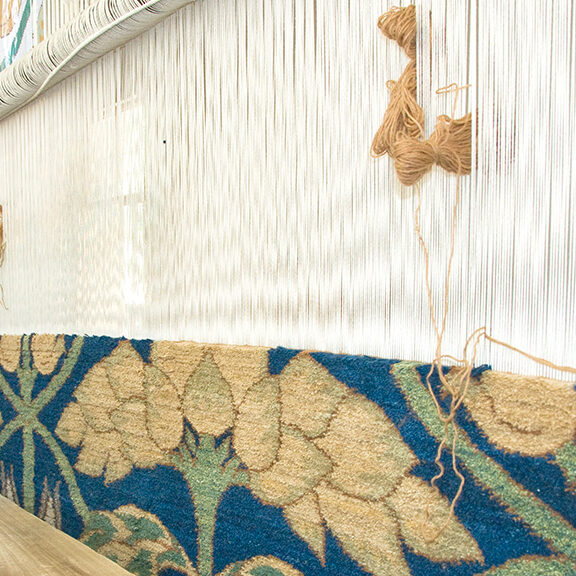
The Thread of Creation: The Art of Handknotted Wool Rugs
A handknotted rug by Orley Shabahang awaits its next knots In the crafting of our fine handknotted wool rugs, throughout the process a variety of artisans demonstrate their mastery. With...
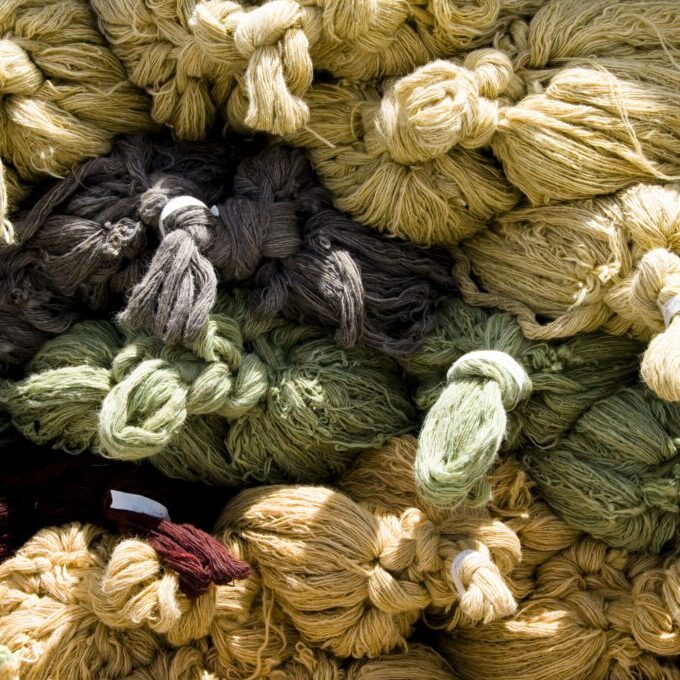
The Thread of Creation: Coloring Wool with Nature’s Palette
Freshly dyed wool shows a spectrum of vibrant hues A forgotten art, it can be easy to ignore the dyes that capture the dazzling tones of nature's palette when coloring...